Une automatisation intelligente pour les flux intralogistiques
Des solutions d'automatisation à chaque étape du processus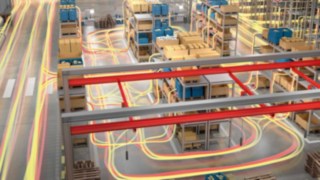
L’intralogistique moderne est confrontée à des défis croissants : le commerce en ligne et l’individualisation de l’offre entraînent une augmentation constante du nombre d’articles et imposent le recours à des processus basés sur des volumes toujours plus réduits. Pour relever ces défis, il est indispensable de disposer de processus correctement structurés. Un flux de matériels efficace et ininterrompu requiert obligatoirement une compréhension parfaite de tous les processus intralogistiques de l’arrivée des marchandises à leur expédition en passant par l’approvisionnement de la production.
Grâce à sa longue expérience en gestion industrielle et en matériel de manutention, Fenwick connaît parfaitement tous les processus clés des flux de matériels. Cette expertise complète nous permet de proposer des optimisations globales dont des systèmes d'automatisation pour lesquels l’efficacité ne dépend pas uniquement de la solution de chariot employée. Pour qu’un processus soit réellement efficace, il est essentiel de mettre en place une automatisation intelligente, au niveau des différentes étapes de processus ou de l’ensemble du flux de matériels. Fenwick vous aide en vous apportant un service de conseil complet, qui analyse la situation de départ sur place dans le détail et développe une solution d'automatisation et de logistique connectée sur mesure à partir des éléments du système existant.
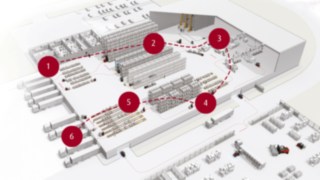
L’efficacité en six étapes
La logistique 4.0 repose sur des flux de matériels correctement structurés et planifiés avec précision. En règle générale, le flux de matériels intralogistique d’une entreprise se compose de six étapes distinctes qui, en raison de leurs exigences spécifiques, offrent des opportunités d’optimisation différentes via l'automatisation.
1. Arrivée des marchandises automatisée
Tout flux de matériels interne commence par le déchargement des marchandises à leur arrivée. Une arrivée de marchandises mal organisée peut entraîner des retards considérables dans la suite des processus. À cette étape, les marchandises sont déchargées, contrôlées, triées, étiquetées et préparées pour le transport dans un entrepôt intermédiaire ou en production. Les principaux critères de réussite sont ici des délais d’exécution réduits, un faible besoin d’espace, le recours à un minimum de collaborateurs et une qualité de processus élevée. Les chariots automatiques Fenwick, tels que les gerbeurs électriques automatiques, contribuent au succès de cette étape.
2. Stockage à l'aide de chariots élévateurs autonomes
Le stockage est le cœur de tout processus intralogistique. Dans l’idéal, il exploite au maximum l’espace de stockage disponible et permet un stockage efficace de marchandises de différentes nature et taille. Dans le même temps, les colis doivent être rapidement et correctement transportés jusqu’à l’emplacement de rayonnage ou de dépôt prévu grâce aux chariots robotisés Fenwick. Des délais d’exécution réduits, un déroulement transparent et une grande flexibilité lors du stockage sont les caractéristiques d’une gestion d’entrepôt bien organisée.
3. Approvisionnement de la production en chariot AGV
Amener les marchandises et les produits au bon endroit au bon moment est le b.a.-ba d’un approvisionnement de production efficace. Qu’il soit automatisé ou manuel, l’approvisionnement de la production et notamment des lignes de montage repose sur différents concepts qui se distinguent par les technologies employées, les niveaux de stockage concernés ou l’organisation des processus mise en place. Dans l’idéal, on obtient des déplacements de marchandises intelligents, gérés sans interruption avec un minimum de consommation d’énergie et de dépenses, notamment grâce à des chariots élévateurs automatisés et électriques Fenwick.
4. Préparation de commandes en chariots autonomes
Un processus de préparation de commandes optimisé peut considérablement accroître la compétitivité d’une entreprise. Les marchandises et produits doivent être regroupés depuis les rayonnages puis préparés de manière rapide et efficace pour que la livraison puisse être réalisée dans les délais. L’ordre de préparation de commandes peut être transmis au préparateur de commandes sous la forme d’une liste de picking analogique ou numérique. Et le préparateur de commandes peut être un être humain ou un chariot automatisé. Afin d’exploiter pleinement le potentiel économique de l’étape de la préparation de commandes, les processus de picking doivent être rapides, précis et traçables. Ce qui est amplement assuré par les chariots autonomes Fenwick.
5. Expédition automatique
L’expédition des marchandises est étroitement liée à la préparation de commandes. Les produits et marchandises doivent être regroupés en un colis prêt à l’envoi afin que le stockage et le transport puissent être organisés le plus harmonieusement possible. Il existe différentes solutions pour optimiser ces processus, notamment en automatisant votre entrepôt et en réduisant ainsi les coûts de transport et d’expédition. Les Warehouse Management Systems de Fenwick sont des logiciels d'automatisation qui permettent de rendre l’ensemble des flux de marchandises plus transparents et plus faciles à gérer.
6. Sortie des marchandises robotisée
La sortie des marchandises correspond à leur mise à disposition hors de l’entrepôt. Après un contrôle de leur identité et de leur qualité, les différents colis sont regroupés en une unité d'expédition et placés dans la zone de mise à disposition. Le cas échéant, d’autres marchandises au contenu inconnu doivent également être intégrées à l’expédition. La moindre erreur lors de la sortie des marchandises peut bloquer l’ensemble des chaînes de processus. À cette étape, il est donc indispensable de disposer d’un flux de marchandises rapide, bien structuré et traçable. Cela est rendu possible grâce aux systèmes automatisés Fenwick.
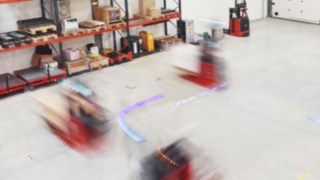
Passez votre entrepôt au niveau supérieur grâce à l’automatisation
L’automatisation peut constituer un élément clé de l’optimisation des flux intralogistiques. Le déploiement de chariots et de solutions automatisés est d’autant plus intéressant que les tâches de transport et de stockage sont répétitives.
Récapitulatif des avantages de l'automatisation
Applications des solutions d’automatisation
Les chariots automatisés peuvent être intégrés aux flux de matériels d’une multitude de façons. En fonction de l’application, ils assument différentes tâches de transport et veillent à ce que les flux de marchandises restent en permanence fluides et sans interruption. Qu’il s’agisse de transport sol à sol, sol à rayonnage ou convoyeur à convoyeur : dans les applications standardisées, les solutions automatisées du type chariot AGV ou AMR sont toujours avantageuses.
Sol à sol
Dans les applications sol à sol automatisées, le chariot élévateur autonome prend la charge au sol et la dépose de nouveau au sol à l’emplacement de destination. Les supports de charge sont placés dans des zones définies pour la préhension et sont transportés jusqu’aux emplacements de destination établis. L’avantage des applications sol à sol est qu’outre un chariot automatisé, aucun autre équipement automatisé n’est nécessaire. Elles peuvent donc être intégrées à presque toutes les étapes du processus intralogistique. Elles peuvent transporter les supports de charge du point d’arrivée des marchandises à l’entrepôt, de l’entrepôt à la production ou de la production à la sortie des marchandises. Les applications au sol sont notamment le choix idéal lorsque de nombreux composants doivent être mis à disposition au bon moment sur un créneau réduit.
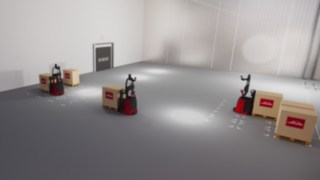
Sol à sol - Projet de référence
C’est chez Fritz Holter GmbH, un grossiste autrichien en sanitaires et systèmes de chauffage, qu’œuvre ce « duo magique » : Franzl et Gustl, comme les ont affectueusement baptisés les collaborateurs. Ces deux chariots de transport automatisés de la série L-MATIC Fenwick fonctionnent en deux équipes et épaulent l’équipe de préparation de commandes du site. En cas de besoin, le préparateur de commandes peut les appeler par simple pression d’un bouton pour une tâche de transport sur les itinéraires rouge ou vert prédéfinis. Franzl ou Gustl se déplace ensuite jusqu’au lieu de dépôt établi en toute autonomie. Pour ce faire, ils empruntent les itinéraires rouge ou vert - un jour l’un, un jour l’autre, sans logiciels complexes. En outre, il n’a pas été nécessaire de modifier l’infrastructure, et les piétons et chariots élévateurs continuent de se déplacer en empruntant les mêmes itinéraires – en toute sécurité. Grâce au travail inlassable de Franzl et Gustl, les collaborateurs peuvent davantage se concentrer sur la préparation de commandes, font ainsi moins d’erreurs, et travaillent globalement plus efficacement. Et la marchandise arrive comme par magie à la destination prévue.
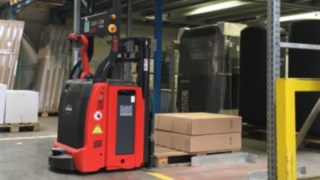
Sol à convoyeur
Les applications sol à convoyeur peuvent intervenir à toutes les étapes du processus intralogistique. À l’arrivée des marchandises, des chariots automatisés prennent les charges au sol et les transportent jusqu’à l’emplacement de stockage prévu. Là, ils transfèrent les marchandises au convoyeur de l’entrepôt. Il peut s’agir d’un entrepôt de pièces entièrement automatisé ou d’un entrepôt grande hauteur doté de chariots pour allées étroites. Une autre application fréquente consiste à ce que les machines autonomes récupèrent les produits finis sur le convoyeur après la production. De là, ils amènent la charge jusqu’à la station de palettisation et d’emballage automatique, l’entrepôt ou directement à la sortie de marchandises, où ils déposent les marchandises sur le sol.
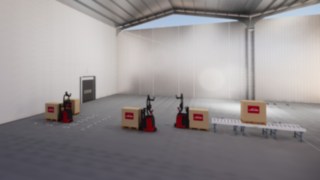
Sol à convoyeur - Projet de référence
Dans les grands entrepôts, les palettes pleines doivent souvent être transportées sur de longs trajets, par exemple pour les transférer de leur lieu de dépôt au convoyeur. Lorsque cette tâche est réalisée manuellement, elle est bien souvent source de perte de temps et de coûts élevés. La solution, bien sûr, c’est l’automatisation. Chez un grand constructeur d’emballages à base de papier dans le sud de l’Allemagne, des chariots de transport autonomes (chariots AGV) transportent la marchandise de manière fiable et sûre d’un point A à un point B, ici un convoyeur. L’AGV repère et place la marchandise sur le convoyeur en toute autonomie. Le seul élément requis pour que cela soit possible, ce sont des rails de centrage installés sur le convoyeur. À l’aide de ces guides, l’AGV dépose la palette automatiquement ou en saisit d’autres pour les transporter à travers l’entrepôt jusqu’à leur destination via un itinéraire fixe.
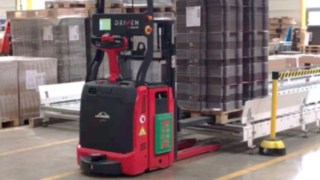
Convoyeur à convoyeur
Les applications convoyeur à convoyeur sont principalement utilisées pour transporter les charges entre les systèmes automatiques fixes. Par exemple, les machines autonomes Fenwick transportent les pièces requises de la sortie de l’entrepôt automatisé à l’accès d’approvisionnement automatique d’une machine de production. Après le processus de production, la marchandise est soit transférée vers l’entrepôt automatique, soit transportée vers l’étape de transformation suivante (p. ex. vers une filmeuse). Enfin, la marchandise passe à l’expédition. Généralement, à cette étape, les chariots de manutention robotisés transfèrent les marchandises à des bandes de convoyage inclinées afin de les attribuer directement à une porte d’expédition ou à un camion de livraison en particulier.
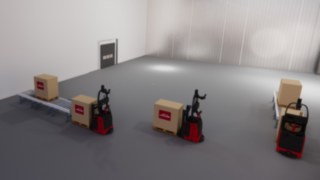
Convoyeur à convoyeur - Projet de référence
La demande explose et la production est multipliée par deux alors que l’infrastructure reste inchangée : c’est précisément dans ce genre de situation que l’automatisation entre en jeu, comme chez Massilly France. Ce fabricant français de matériel d’emballage était à la recherche d’une solution afin de transporter ses marchandises de manière automatique et sûre. Et il l’a trouvée : un gerbeur automatique L-MATIC Fenwick transporte les palettes du robot de palettisation automatique à la filmeuse automatique, attend que les cartons soient filmés et les transporte ensuite jusqu'à l’entrepôt. « La solution du L-MATIC de Fenwick est très intéressante pour nous car elle évolue en permanence, sans nous obliger à modifier notre infrastructure, explique Patrice Ferrero, Responsable production chez Massilly France. Grâce à leur facilité d’utilisation et aux recharges intermédiaires flexibles, les chariots de manutention AGV ont pu être intégrés aux processus existants en toute fluidité, et permettent désormais à Massilly France de laisser tourner la production à plein régime. Aujourd’hui, 4 chariots électriques AGV sont déployés, et de nouvelles intégrations sont prévues.
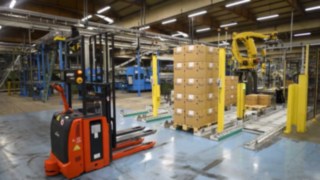
Transfert convoyeur vers racks
Les applications de transfert de charges de convoyeurs vers des rayonnages sont généralement employées lorsqu’un stockage intermédiaire des marchandises est nécessaire afin d’assurer l’approvisionnement continu des machines de production. Les chariots automatisés transportent les pièces requises du rayonnage de l’entrepôt intermédiaire jusqu’au convoyeur placé devant les machines de production. Ensuite, ils assurent le transport de retour de la production au rayonnage. Là, les pièces sont de nouveau stockées quelque temps avant de quitter l’entrepôt. Les applications de convoyeurs vers des rayonnages sont généralement employées par les sous-traitants automobiles afin d’aligner précisément leurs livraisons au rythme de production des constructeurs automobiles. Dans l’industrie de l’emballage, les produits finis sont transportés du convoyeur de fin de production à la zone d’expédition, où ils sont déposés sur des racks dynamiques ou classiques pour pouvoir ensuite être récupérés.
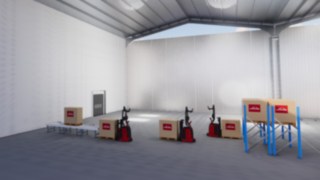
Sol à rayonnage
Les applications sol à rayonnage sont très largement employées. Elles interviennent généralement à l’arrivée des marchandises, afin de les stocker sur les rayonnages. Depuis l’entrepôt, elles servent ensuite à transporter les marchandises jusqu’à des emplacements au sol où des collaborateurs viendront les récupérer. Les applications sol à rayonnage sont particulièrement flexibles et polyvalentes dans la mesure où aucun équipement spécifique n’est requis afin de placer les marchandises sur le sol. La marchandise peut également être transportée vers un autre rayonnage pour un stockage intermédiaire. Cette possibilité est généralement employée lorsqu’il s’agit d’assurer l’approvisionnement rapide de machines de production, même si l’entrepôt principal se trouve loin du lieu de transformation.
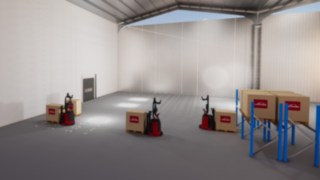