L’automatisation chez Massilly
Le plus naturel du monde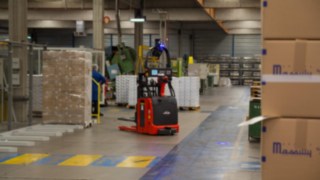
L’usine principale du fabricant français d’emballages métalliques Massilly à Cluny joue la carte d’une automatisation maximale pour sa production. La dernière étape du processus, le transport des palettes dans l’entrepôt, était jusqu’à maintenant réalisé manuellement. Cette tâche est désormais assumée avec brio par des chariots automatisés : des représentants d’entreprises viennent même sur place pour se convaincre des atouts des AGV Fenwick.
Les boîtes de conserve vides font des montagnes russes. Des pièces métalliques brillantes et argentées traversent le grand hall de production sur d'interminables tapis roulants. Au milieu de tout cela, des machines entièrement automatisées prennent en charge le travail de détail : l’emboutissage des couvercles, la mise en forme de fines tôles, le soudage, l’impression. C’est un flot permanent de cognements, sifflements, martèlements et vrombissements jusqu’à ce que le produit fini soit rangé sur des palettes.
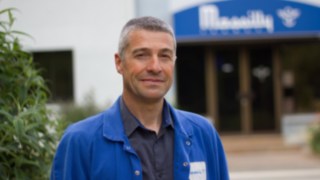
Christophe Marteau, en charge de la technologie et du développement chez Massilly en tant que CTO
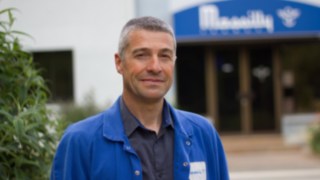
Christophe Marteau, en charge de la technologie et du développement chez Massilly en tant que CTO
Une boîte de conserve, cela semble très simple de prime abord. Et pourtant, il s’agit d’un objet du quotidien extrêmement complexe techniquement parlant.
Christophe Marteau maîtrise parfaitement ses gestes : chaque boîte doit présenter des dimensions précises, résister à la stérilisation et répondre à des exigences clés dans le domaine de la résistance mécanique. Pour assurer la qualité de leurs produits, Massilly fait appel à des spécialistes de différentes spécialités, des ingénieurs aux chimistes.
Depuis des années, l’entreprise mise résolument sur l’automatisation. « Pour nous distinguer de la concurrence des pays émergents, nous n’avons pas une infinité de possibilités à disposition ». La qualité en fait partie. L’autre solution est d’établir une production parfaitement agile et fluide. « Peut-être que l’automatisation ne crée pas de nouveaux emplois », concède-t-il « mais elle sécurise ceux qui existent déjà ». Se tenant à quelques pas d’une station d’emballage, M. Marteau nous explique qu’une usine qui n’investirait pas dans l’innovation serait condamnée, tôt ou tard, à disparaitre.
Une machine de palettisation prend les cartons remplis de produits finis et compose la palette. À côté, un gerbeur automatisé attend sa prochaine commande. Outre l’équipement de série habituel, ce chariot est équipé d’un laser de navigation, de capteurs de sécurité, d’une unité de calcul, d’un écran tactile et d’un Blue Spot. Dès que le bras robotisé termine une palette, le Fenwick L-MATIC libère automatiquement la sortie de la machine de palettisation, attrape la palette et la dépose à quelques mètres de là sur une filmeuse automatique. Ensuite, un processus similaire s’enchaîne : le L-MATIC reprend la palette de la filmeuse et se dirige vers l’entrée de l'entrepôt à haut rayonnage. C’est là que l’humain intervient pour la première fois. Les caristes récupèrent les palettes et les stockent.
« Ces appareils nous apportent une flexibilité maximale »
L'usine principale de Massilly se situe au cœur du Mâconnais, une région fertile et vallonnée bordée de nombreuses forêts et vignes. Le business model de fabrication de boîtes et de couvercles en fer blanc recyclé a commencé dans les années 50. Aujourd’hui, Massilly exploite 20 usines dans 18 pays et emploie 1 300 collaborateurs dans le monde. L’entreprise est leader du marché français de la fabrication de couvercles en tôle, et numéro trois mondial. Thomas Bindschedler représente la quatrième génération de la famille à la tête de l’entreprise. Massilly est un « Hidden Champion » au sens le plus littéral du terme. Du leader italien du marché des pâtes aux spécialistes de la peinture industrielle, de nombreux fabricants d’articles de marque font confiance à l’entreprise française pour leurs emballages.
« Mais n’aurait-on pas pu tout simplement, relier la station d’emballage et l’entrepôt de marchandises à l’aide d’un tapis roulant ? », Christophe Marteau secoue la tête : « On aurait pu, mais dans ce cas des voies importantes auraient été bloquées ! Les appareils Fenwick robotics nous apportent une flexibilité maximale. Nous pouvons adapter les trajectoires à tout moment. » Grâce à la géonavigation, les gerbeurs autonomes sont capables de s’orienter dans l’espace en toute autonomie. Ils n'ont besoin ni de réflecteurs lasers, ni de rails, ni d'aimants ou d'autres accessoires.
Ils utilisent simplement les particularités de la pièce, comme les murs, les rayonnages ou les colonnes comme points de référence pour s’orienter.
Le chariot élévateur connaît la structure de l’usine et réagit en temps réel quand, par exemple, un collaborateur traverse la voie
De plus, les personnes qui travaillent dans l’entrepôt sont régulièrement formées pour savoir comment se comporter vis-à-vis des chariots élévateurs automatisés et ont été informées à l’avance de la mise en place de ces chariots et associées au projet, explique Christophe Marteau. Les processus automatiques font désormais partie du quotidien chez Massilly.
C’est le cas aussi des deux employés qui se trouvent à l’autre extrémité du hall de production, près d’une seconde station de chargement. Un lieu qui fait penser aux stands de course automobile avec ses emplacements de parking. Un gerbeur Fenwick L-MATIC de dernière génération se déplace en clignotant, effectue un virage, pivote sur lui-même et charge sur sa fourche une palette contenant des boîtes à biscuits colorées. Les deux collaborateurs de l'entrepôt surveillent attentivement l'opération. « Nous venons d’effectuer une modification sur la machine à filmer. Les opérateurs contrôlent que tout fonctionne à nouveau comme il faut », explique M. Marteau. Les deux premiers gerbeurs automatisés ont été mis en service en 2012. Début 2016, la flotte a été complétée de deux nouveaux chariots L-MATIC.
Dans un premier temps, il s’agissait de gagner en productivité pour répondre à une demande croissante. En 2011, Massilly produisait 1,5 milliard de couvercles, trois ans plus tard ce chiffre s’approche déjà de la barre des deux milliards. Christophe Marteau s’est rendu compte du potentiel d’innovation des chariots automatisés et était déterminé à les utiliser :
il s’agissait d’un investissement d’avenir
« Y compris du point de vue de notre état d’esprit. Le fait que nous exploitions aujourd’hui deux fois plus de chariots autonomes montre à quel point nous sommes convaincus d’avoir pris la bonne décision », affirme Christophe Marteau.
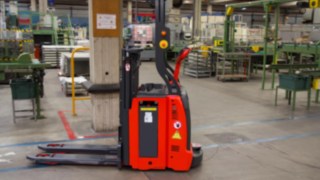
Un chariot automatisé Fenwick en action chez Massilly
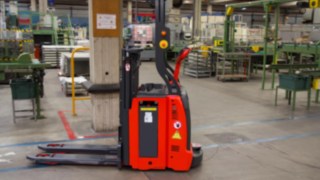
Un chariot automatisé Fenwick en action chez Massilly
Un chariot élévateur intelligent ne se trompe jamais
Aujourd’hui, le transport est plus fluide, et le nombre d’accidents a diminué de manière significative. « Car les AGV Fenwick sont constants, tout simplement fiables », souligne Christophe Marteau. « Les chariots conduits par des humains demandent en permanence la plus grande concentration pour les déplacements, les manœuvres ou l’appréciation de la vitesse – et lorsqu’une palette tombe, tous les cartons doivent être déballés et tous les couvercles contrôlés un par un. Cela coûte un temps précieux. Le robot quant à lui ne se trompe jamais. » Des personnes intéressées du monde entier rendent visite à Massilly à Cluny pour découvrir la solution et interroger Christophe Marteau sur son expérience. En effet, les chariots robotisés assument de nombreuses tâches standardisées qui peuvent être transposées à d’autres domaines.
« Notre entrepôt de stockage se prête également très bien au déploiement de chariots industriels automatiques », remarque Christophe Marteau. Un déploiement serait actuellement à l’étude. Le transstockeur robotique K-MATIC que Fenwick a annoncé pour la fin de l’année pourrait être la solution idéale.